teamzr1
Supporting vendor
Charlie Burga retired in December 2011 after a 42-year career with a major medical company. He was healthy, financially secure, and ready to stop working, but there was one dilemma. “I did a good job of planning my retirement from a financial perspective,” he recalls, “but I didn’t really have a plan about what I would do with all of that found time.”
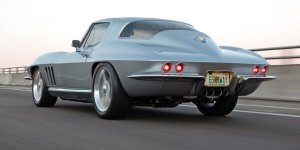
Any danger of boredom was quickly obviated, however, when a pal inspired Burga by example.
“A friend was in the middle of building a C2 restomod and that caught my eye,” he says. “He encouraged me to build a custom Corvette based on my experience restoring my ’65 convertible.”
Burga had enjoyed refurbishing the Midyear in question but wasn’t especially keen on repeating the process.
“The car I restored has loud side pipes and no air conditioning,” he tells us, “so it’s lots of fun for the first hour.
After that my six-foot, five-inch frame starts getting leg pains, my ears ring, and the sweat runs down my back.”
After seeing what his friend was doing, Burga resolved to build a classic Corvette with the comfort of a new model.
Burga considers C2 coupes the most beautiful Corvettes ever designed, so he began searching for a suitable Sting Ray to build the car of his dreams. After a few months of looking he found an excellent specimen in a small mountain community outside of Denver. It was a ’65 coupe that had been disassembled three years prior by a man planning to build a mild hot rod.
He got as far as taking everything apart and accumulating lots of new parts including a full interior from Al Knoch, chrome bumpers, an Ididit tilt steering column, a ’67 big-block hood, parking and taillight assemblies, door handles, and so on but then the project stalled and he lost interest.
The disassembled car was an excellent launching pad for a modernized Midyear, but there was one thing that gave Burga pause initially. “This was an original fuel-injected car,” he says, “so I felt bad that it wouldn’t be restored as such.” His feelings of guilt were assuaged, however, when he learned that the car’s owner had already sold the entire FI system and rebuilt the car’s 327 engine with non-stock parts.
Burga had already mapped out his build plan and knew he’d install an LS3, so he had no use for the hot-rodded small-block. Fortunately, the seller was willing to keep the engine and lower the car’s price accordingly.
After the deal was finalized, Burga had one more challenge before heading back home to Florida: He had to prepare his newly acquired and completely disassembled car for shipping.
“Before I left Colorado I managed to build a wooden dolly with caster wheels and attach it under the body and bare frame,” he recalls. “At least the car could then be pushed around.”
His efforts yielded the desired result, and in January 2013 the car and all of its parts were delivered to his residence in Fort Lauderdale.
To fulfill his vision for a mostly stock-appearing car with upgraded performance and amenities, Burga bought an SRIII Motorsports tubular chassis fitted with C5 front and C4 rear suspension parts, a C4 Dana 36 differential fitted with 3.08:1 gears, C4 rack-and-pinion steering, C5 disc brakes, and Viking two-way adjustable coil-overs at all four corners.
He then completed the assembly with custom-bent, stainless-steel fuel and brake lines.
Propulsion comes from an LS3 Burga bought new in 2014.
Out of the box, this smooth-running and clean-burning engine delivers 436 net horsepower at 5,900 rpm and 428 lb-ft of torque at 4,600 rpm (as installed in a C6). Besides providing considerably more output than the car’s original 375-horse (gross) Fuelie engine, the LS3 offers countless other benefits, including quicker response, a much broader power band, better thermal stability, and less mass.
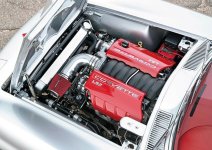
For optimum packaging, Burga went with a Vintage Air polished front-runner drive system.
Thanks to its compact alternator, power-steering pump, and A/C compressor, the setup fit the C2 engine compartment without issue.
Exhaust from the LS3 is channeled through stock manifolds to custom, 2.5-inch steel pipes and low-restriction Magnaflow mufflers. Equipped with custom resonators, the system provides a deep, throaty exhaust note that Burga says is subdued enough for long trips
The all-aluminum engine is coupled to a ProFit3 Tremec five-speed gearbox from American Powertrain. Unlike the four-speed the ’65 originally came with, this modern transmission offers a sufficient gear-ratio range to facilitate both off-the-line launches and low-rpm highway cruising. Inside the car, the stock look Burga wanted is preserved with an original-style shifter designed to work with the Tremec box. Shifting, meanwhile, is noticeably improved compared with a stock Midyear by virtue of an American Powertrain hydraulic-clutch system.
While his SRIII chassis was under construction, Burga went to work on the car’s body. After building another wooden dolly high enough to allow him to work underneath it, he put in a lot of hours using a heat gun and scraper to remove a thick, tar-like undercoating that someone had assiduously applied to the underside. Once that task was completed, he executed a series of well-conceived modifications designed to make the car more comfortable for his long frame.
“I cut out the driver-side foot well and re-glassed it to remove the angle,” he explains. “The firewall is now just straight down, which adds about five inches of additional floor space.
Other alterations were required in order for the body to work with the new chassis. “I had to do some cutting and re-glassing of the front inner fenders to accommodate the C5 A-arm suspension,” Burga says, “and I cut out the storage wells behind the seats and flattened the rear floor to provide clearance for the C4 suspension and C6 wheels.”
To improve the car’s cosmetics, Burga removed and glassed over the side vents behind each door for a cleaner look. He used a similar treatment on the hole for the factory antenna, which was no longer needed thanks to the new antenna installed inside the ceiling above the passenger door. He also cut out the firewall indentation that housed the windshield wiper motor and glassed over the hole to leave a flat firewall.
Finally, he modified the rear valance to accommodate four exhaust tips beneath the license-plate area.
To make sure there was sufficient clearance for the suspension, steering, and wheels the latter of which are shod with 255/45ZR18 Michelin Pilot Sport 4S tires all around the body was installed onto the chassis several times while the fiberglass work was being performed. The repeated installations and removals also enabled Burga to perfect the fit of the door and hood.
When purchased, the car was wearing white paint that Burga had no intention of reusing. The normally unpleasant and time-consuming task of removing it was simplified when Burga discovered that he could gently scrape the finish off with a razor blade. “I didn’t want to bead blast for fear of body damage, and I thought chemical strippers could seep into the fiberglass and remain there, so I decided to use razors.
Once I developed my technique, it was easy—the paint came right off and left all the primer.”
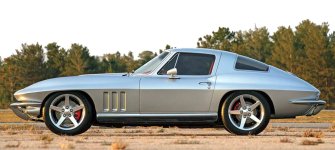
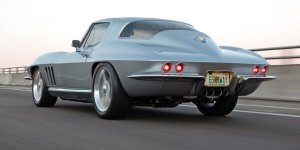
Any danger of boredom was quickly obviated, however, when a pal inspired Burga by example.
“A friend was in the middle of building a C2 restomod and that caught my eye,” he says. “He encouraged me to build a custom Corvette based on my experience restoring my ’65 convertible.”
Burga had enjoyed refurbishing the Midyear in question but wasn’t especially keen on repeating the process.
“The car I restored has loud side pipes and no air conditioning,” he tells us, “so it’s lots of fun for the first hour.
After that my six-foot, five-inch frame starts getting leg pains, my ears ring, and the sweat runs down my back.”
After seeing what his friend was doing, Burga resolved to build a classic Corvette with the comfort of a new model.
Burga considers C2 coupes the most beautiful Corvettes ever designed, so he began searching for a suitable Sting Ray to build the car of his dreams. After a few months of looking he found an excellent specimen in a small mountain community outside of Denver. It was a ’65 coupe that had been disassembled three years prior by a man planning to build a mild hot rod.
He got as far as taking everything apart and accumulating lots of new parts including a full interior from Al Knoch, chrome bumpers, an Ididit tilt steering column, a ’67 big-block hood, parking and taillight assemblies, door handles, and so on but then the project stalled and he lost interest.
The disassembled car was an excellent launching pad for a modernized Midyear, but there was one thing that gave Burga pause initially. “This was an original fuel-injected car,” he says, “so I felt bad that it wouldn’t be restored as such.” His feelings of guilt were assuaged, however, when he learned that the car’s owner had already sold the entire FI system and rebuilt the car’s 327 engine with non-stock parts.
Burga had already mapped out his build plan and knew he’d install an LS3, so he had no use for the hot-rodded small-block. Fortunately, the seller was willing to keep the engine and lower the car’s price accordingly.
After the deal was finalized, Burga had one more challenge before heading back home to Florida: He had to prepare his newly acquired and completely disassembled car for shipping.
“Before I left Colorado I managed to build a wooden dolly with caster wheels and attach it under the body and bare frame,” he recalls. “At least the car could then be pushed around.”
His efforts yielded the desired result, and in January 2013 the car and all of its parts were delivered to his residence in Fort Lauderdale.
To fulfill his vision for a mostly stock-appearing car with upgraded performance and amenities, Burga bought an SRIII Motorsports tubular chassis fitted with C5 front and C4 rear suspension parts, a C4 Dana 36 differential fitted with 3.08:1 gears, C4 rack-and-pinion steering, C5 disc brakes, and Viking two-way adjustable coil-overs at all four corners.
He then completed the assembly with custom-bent, stainless-steel fuel and brake lines.
Propulsion comes from an LS3 Burga bought new in 2014.
Out of the box, this smooth-running and clean-burning engine delivers 436 net horsepower at 5,900 rpm and 428 lb-ft of torque at 4,600 rpm (as installed in a C6). Besides providing considerably more output than the car’s original 375-horse (gross) Fuelie engine, the LS3 offers countless other benefits, including quicker response, a much broader power band, better thermal stability, and less mass.
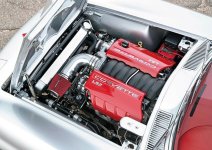
For optimum packaging, Burga went with a Vintage Air polished front-runner drive system.
Thanks to its compact alternator, power-steering pump, and A/C compressor, the setup fit the C2 engine compartment without issue.
Exhaust from the LS3 is channeled through stock manifolds to custom, 2.5-inch steel pipes and low-restriction Magnaflow mufflers. Equipped with custom resonators, the system provides a deep, throaty exhaust note that Burga says is subdued enough for long trips
The all-aluminum engine is coupled to a ProFit3 Tremec five-speed gearbox from American Powertrain. Unlike the four-speed the ’65 originally came with, this modern transmission offers a sufficient gear-ratio range to facilitate both off-the-line launches and low-rpm highway cruising. Inside the car, the stock look Burga wanted is preserved with an original-style shifter designed to work with the Tremec box. Shifting, meanwhile, is noticeably improved compared with a stock Midyear by virtue of an American Powertrain hydraulic-clutch system.
While his SRIII chassis was under construction, Burga went to work on the car’s body. After building another wooden dolly high enough to allow him to work underneath it, he put in a lot of hours using a heat gun and scraper to remove a thick, tar-like undercoating that someone had assiduously applied to the underside. Once that task was completed, he executed a series of well-conceived modifications designed to make the car more comfortable for his long frame.
“I cut out the driver-side foot well and re-glassed it to remove the angle,” he explains. “The firewall is now just straight down, which adds about five inches of additional floor space.
Other alterations were required in order for the body to work with the new chassis. “I had to do some cutting and re-glassing of the front inner fenders to accommodate the C5 A-arm suspension,” Burga says, “and I cut out the storage wells behind the seats and flattened the rear floor to provide clearance for the C4 suspension and C6 wheels.”
To improve the car’s cosmetics, Burga removed and glassed over the side vents behind each door for a cleaner look. He used a similar treatment on the hole for the factory antenna, which was no longer needed thanks to the new antenna installed inside the ceiling above the passenger door. He also cut out the firewall indentation that housed the windshield wiper motor and glassed over the hole to leave a flat firewall.
Finally, he modified the rear valance to accommodate four exhaust tips beneath the license-plate area.
To make sure there was sufficient clearance for the suspension, steering, and wheels the latter of which are shod with 255/45ZR18 Michelin Pilot Sport 4S tires all around the body was installed onto the chassis several times while the fiberglass work was being performed. The repeated installations and removals also enabled Burga to perfect the fit of the door and hood.
When purchased, the car was wearing white paint that Burga had no intention of reusing. The normally unpleasant and time-consuming task of removing it was simplified when Burga discovered that he could gently scrape the finish off with a razor blade. “I didn’t want to bead blast for fear of body damage, and I thought chemical strippers could seep into the fiberglass and remain there, so I decided to use razors.
Once I developed my technique, it was easy—the paint came right off and left all the primer.”
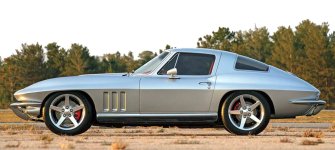