A quick update on the rear lights ...
The two 'holes' for the drivers side rear light assemblies were both very badly damaged. It looked like the last person to work on this area removed the lights used a hammer without undoing the fixing nuts so some repair work was necessary.
The four rear light base units were cleaned up and painted.
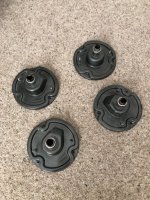
I forgot to take a picture of the damage but a good portion of the rear surface that the light base butts up to was missing - most of what you can see that is grey on the back surface is new material. Three layers of glass fibre were used to patch the damaged area.... and the two mounting holes and the centre keyhole shaped err... hole was cut out with a multitool after carefully taking a template from the passenger side.
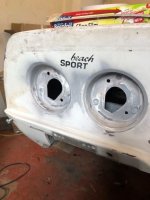
And lastly with a rear light base for a test fit.
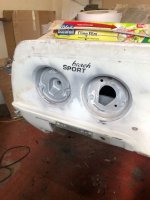
I think that 'Beach Sport' logo will have to go. A pity as (to my mind) its very reminiscent of the 70's/80's era and definitely in keeping with this car's Vero Beach (FLA) home in the US . A bit naff too - especially for Eastbourne.
The two 'holes' for the drivers side rear light assemblies were both very badly damaged. It looked like the last person to work on this area removed the lights used a hammer without undoing the fixing nuts so some repair work was necessary.
The four rear light base units were cleaned up and painted.
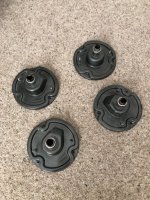
I forgot to take a picture of the damage but a good portion of the rear surface that the light base butts up to was missing - most of what you can see that is grey on the back surface is new material. Three layers of glass fibre were used to patch the damaged area.... and the two mounting holes and the centre keyhole shaped err... hole was cut out with a multitool after carefully taking a template from the passenger side.
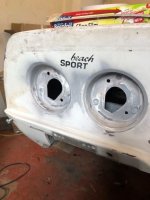
And lastly with a rear light base for a test fit.
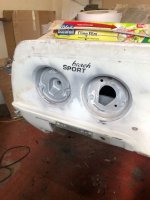
I think that 'Beach Sport' logo will have to go. A pity as (to my mind) its very reminiscent of the 70's/80's era and definitely in keeping with this car's Vero Beach (FLA) home in the US . A bit naff too - especially for Eastbourne.